ปฐมบทของการพัฒนาชิ้นส่วนรถไฟเพื่อทดแทนการนำเข้า
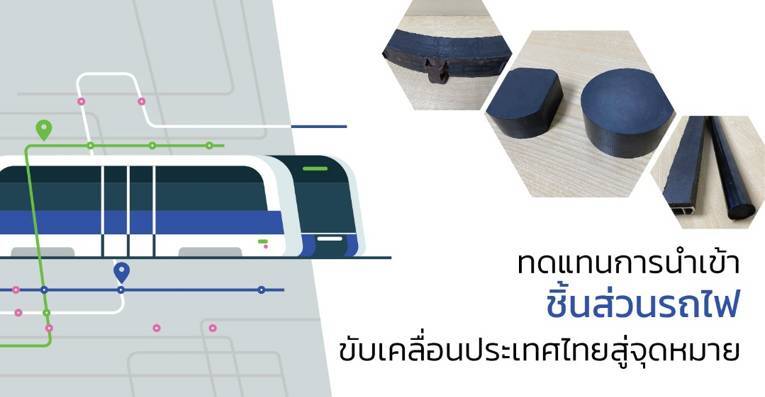
สัมภาษณ์และเรียบเรียงโดย งานสื่อสารและขับเคลื่อนความรู้
ฝ่ายเผยแพร่เทคโนโลยีวัสดุ
คุณภาณุ เวทยนุกูล และคณะทีมวิจัยเทคโนโลยีกระบวนการผลิตวัสดุผง กลุ่มวิจัยกระบวนการทางวัสดุและการผลิตอัตโนมัติ ศูนย์เทคโนโลยีโลหะและวัสดุแห่งชาติ (เอ็มเทค) ได้วิจัยและพัฒนาชิ้นส่วนรถไฟเพื่อทดแทนการนำเข้า ได้แก่ แท่งหล่อลื่นบังใบล้อแบบของแข็ง แหนบรับไฟสำหรับรถไฟฟ้า และแผ่นเบรกรถไฟ ชิ้นส่วนที่พัฒนาขึ้นนี้จุดมุ่งหมายให้มีคุณภาพและสมรรถนะการใช้งานตามมาตรฐานสากล เพื่อให้ประเทศไทยสามารถพึ่งพาตนเองได้มากขึ้น
ระบบโครงข่ายรถไฟที่มีประสิทธิภาพและครอบคลุมทั่วทุกภูมิภาคของประเทศจะช่วยให้ผู้คนจำนวนมากเดินทางคล่องตัวสะดวกสบาย ในปัจจุบัน (พ.ศ. 2566) เรามีรถไฟฟ้า BTS และ MRT ในกรุงเทพมหานคร และมีรถไฟเชื่อมโยงหลายพื้นที่ในส่วนภูมิภาค และคาดว่ารถไฟความเร็วสูงในบางเส้นทางคงอีกไม่นานเกินรอ
การมีรถไฟและรถไฟฟ้าที่มีจำนวนเส้นทางและระยะทางวิ่งที่เพิ่มมากขึ้น ย่อมทำให้อุปสงค์ของอุปกรณ์และชิ้นส่วนต่างๆ ของระบบรางเพิ่มขึ้นอย่างมีนัยสำคัญ การพัฒนาการผลิตชิ้นส่วนดังกล่าวจึงมีความสำคัญอย่างมากต่ออุตสาหกรรมรถไฟไทย ระบบรางรถไฟของประเทศจะยั่งยืนได้ต้องอาศัยรากฐานของอุตสาหกรรมระบบรางในประเทศที่เข้มแข็ง อย่างไรก็ดีอุตสาหกรรมรางไทยในปัจจุบันผู้ประกอบการยังมีจำนวนน้อยราย ทั้งยังขาดความพร้อมในด้านความสามารถเชิงการแข่งขัน ดังนั้น นโยบายส่งเสริมการผลิตชิ้นส่วนในประเทศ (local content ) สำหรับระบบรางจึงนับเป็นปัจจัยสำคัญที่จะช่วยวางรากฐานด้านความมั่นคงและความยั่นยืนของระบบรางไทยในอนาคต
คนเหล็กผู้เห็นโอกาส
คุณภาณุ เวทยนุกูล นักวิจัยซึ่งคลุกคลีในแวดวงอุตสาหกรรมชิ้นส่วนโลหะมาอย่างยาวนาน ได้เล็งเห็นโอกาสในการต่อยอดการประยุกต์ใช้เทคโนโลยีกระบวนการผลิตวัสดุผงและเทคโนโลยีที่เกี่ยวข้อง เพื่อพัฒนาสิ้นส่วนรถไฟ เสริมสร้างศักยภาพอุตสาหกรรมรถไฟไทยให้สามารถพัฒนาชิ้นส่วนรถไฟทดแทนการนำเข้าจากต่างประเทศได้
คุณภาณุกล่าวถึงระยะเวลาอันยาวนานกว่าหนึ่งร้อยปีที่ระบบขนส่งทางรางของไทยได้ถือกำเนิดขึ้นว่า “ประเทศซึ่งกิจการรถไฟมีอายุยาวนานขนาดนี้ แต่เรากลับมีองค์ความรู้เกี่ยวกับชิ้นส่วนสมัยใหม่ และความสามารถที่จะพึ่งพาตนเองได้ไม่มากนัก แตกต่างจากอุตสาหกรรมยานยนต์และชิ้นส่วนยานยนต์ของไทย ที่ถือเป็นหนึ่งในศูนย์กลางการผลิตที่สำคัญและมีชื่อเสียงระดับโลก แต่สำหรับอุตสาหกรรมการผลิตชิ้นส่วนรถไฟของเรา ข้อเท็จจริงคือ ทุกวันนี้ชิ้นส่วนรถไฟรุ่นใหม่ๆ ส่วนใหญ่เรายังต้องพึ่งพาอุตสาหกรรมการผลิตจากต่างประเทศเป็นหลัก”
อย่างไรก็ดี คุณภาณุ มองว่า “เรายังมีความหวัง โดยตลอดหลายปีที่ผ่านมา จะเห็นว่ารัฐบาลได้ให้ความสำคัญอย่างมากต่อการลงทุนระบบรางเพื่อเชื่อมต่อโครงข่ายการเดินทาง และไม่เพียงแต่มุ่งหวังให้ครอบคลุมทั่วทุกภูมิภาคเท่านั้น แต่เป้าหมายข้างหน้ายังเล็งถึงการที่ประเทศไทยจะต้องเป็นศูนย์กลางผลิตชิ้นส่วน อะไหล่ ไปจนถึงขบวนรถ เพื่อลดต้นทุนลดการพึ่งพิงการนำเข้าวัสดุอุปกรณ์จากต่างประเทศ โดยมีหลายหน่วยงานที่เกี่ยวข้องได้จับมือร่วมมือกัน เพื่อพัฒนาอุตสาหกรรมระบบรางของไทยให้มีความยั่งยืน ส่งเสริมและสนับสนุนให้มีการผลิตชิ้นส่วนในประเทศ การถ่ายทอดเทคโนโลยี พัฒนาบุคลากร วิจัยและพัฒนาต่อยอดอุตสาหกรรมทั้งระบบ ตามนโยบายไทยทำ ไทยใช้ คนไทยต้องได้รับประโยชน์ (Thai First)”
ตีเหล็กเมื่อร้อน
เมื่อเห็นสัญญาณและนโยบายที่ชัดเจนของทางภาครัฐ คุณภาณุและทีมวิจัยจึงไม่รีรอที่จะเริ่มต้นและต่อยอดการประยุกต์ใช้เทคโนโลยีฐานของเอ็มเทคที่มีอยู่ ไปสู่การวิจัยและพัฒนาชิ้นส่วนทดแทนสำหรับอุตสาหกรรมรถไฟ โดยได้ประสานงานกับการรถไฟแห่งประเทศไทย เพื่อนำเสนอแนวความคิดและแสดงความพร้อมในการร่วมพัฒนาชิ้นส่วนรถไฟ เพื่อช่วยลดภาระการพึ่งพาหรือการนำเข้าเทคโนโลยีต่างชาติ โดยเฉพาะในช่วงเดินรถและบำรุงรักษา (Operation and Maintenance, O&M) ซึ่งในระยะยาวพบว่าภาระค่า O&M มักสูงกว่ามูลค่าการก่อสร้างเริ่มต้นหลายเท่าตัว
คุณภาณุ ได้เล่าถึงจุดเริ่มต้นของการวิจัยและพัฒนาชิ้นส่วนรถไฟทดแทนว่า “ทีมงานได้คัดเลือกชิ้นส่วนรถไฟจำนวน 3 ชิ้น ที่เราเล็งเห็นศักยภาพและความเป็นไปได้ในการดำเนินการนำร่อง ทั้งในแง่การใช้งานและความพร้อมของเทคโนโลยีและการผลิตที่มีในประเทศ ชิ้นส่วนรถไฟทั้ง 3 ชิ้นส่วนนั้นประกอบด้วย (1) แท่งหล่อลื่นบังใบล้อแบบของแข็งสำหรับระบบราง (Solid lubricant sticks) (2) ชิ้นส่วนตัวนำคาร์บอนของแหนบรับไฟสำหรับรถไฟฟ้า (Carbon strip of pantograph for electrical trains) และ (3) แผ่นเบรกรถไฟจากวัสดุเชิงประกอบเนื้อทองแดง (Brake pads from sintered self-lubricating composites)”
เริ่มต้นกับชิ้นส่วนรถไฟของคนไทย
สำหรับคนทั่วไปแล้วชิ้นส่วนอุปกรณ์เหล่านี้คงไม่คุ้นหู แต่มันเป็นชิ้นส่วนที่สำคัญอย่างยิ่งและใช้งานในปริมาณมาก คุณภาณุเริ่มต้นเล่าถึงชิ้นส่วนชิ้นแรก ดังนี้
“เริ่มที่ชิ้นส่วนรถไฟชิ้นแรก คือ แท่งหล่อลื่นบังใบล้อ แต่ก่อนอื่นคงต้องรู้จัก ‘บังใบล้อ’ ก่อน ศัพท์แปลกๆ คำนี้ในภาษาอังกฤษเรียกว่า wheel flange หากก้มลงมองล้อรถไฟจากด้านหน้ารถ เราจะพบว่าบริเวณส่วนล้อที่สัมผัสกับรางนั้นไม่ได้เรียบเสมอกันทั้งหมด แต่มีช่วงขอบด้านนอกของล้อที่ยื่นโค้งออกมาคล้ายครีบ ซึ่งทำหน้าที่ประหนึ่งตัวบังคับล้อให้ล้อนั้นไหลไปตามรางรถไฟและไม่หลุดตกรางขณะที่รถไฟวิ่งด้วยความเร็วสูงหรือเข้าโค้ง บริเวณจุดส่วนโค้งเว้าดังกล่าวของล้อซึ่งสัมผัสกับรางจะเกิดภาระการรับแรงและการเสียดสีมากที่สุด นี่เป็นสาเหตุที่ต้องมีการหล่อลื่นเพื่อช่วยลดการเสียดสีและยืดอายุของทั้งล้อรถไฟและรางรถไฟที่ตำแหน่งดังกล่าว อุปกรณ์หล่อลื่นที่ว่านี้คือ แท่งหล่อลื่น (lubricant sticks) ซึ่งทำหน้าที่เสมือนเป็นลิปมันแต้มฟิล์มบางๆ เคลือบบนล้อ เพื่อช่วยลดแรงเสียดทานมหาศาลที่เกิดขึ้นขณะสัมผัสกับรางรถไฟ”
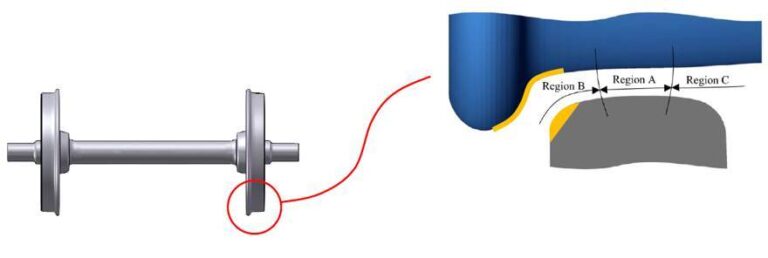
ตำแหน่งบังใบล้อที่เกิดการเสียดสีจากแรงกดทับและแรงเฉือน
คุณภาณุเล่าว่า “ชิ้นส่วนสิ้นเปลืองเหล่านี้เป็นชิ้นส่วนที่เป็นที่ต้องการและต้องใช้จำนวนมาก แต่คนไทยกลับมีความรู้กับเจ้าสิ่งนี้น้อยมาก เรานิยมเรียกมันกันว่า carbon stick เพราะลักษณะภายนอกเป็นสีดำ แต่แท้ที่จริงชิ้นส่วนนี้ที่เรานำเข้าจากต่างประเทศนั้นทำมาจากโมลิบดีนัมไดซัลไฟด์ (molybdenum disulfide)”
“วัสดุที่นำเข้ามา มีคุณสมบัติและการใช้งานที่เหมาะกับเขตอากาศหนาวเย็นและแห้งตามเขตภูมิศาสตร์ที่ตั้งของประเทศผู้ผลิต แต่ด้วยลักษณะสภาพภูมิอากาศในเขตร้อนชื้นของไทย ไม่ว่าจะเป็นฟ้าฝนที่ตกชุก หรืออากาศที่ร้อนชื้นอบอ้าวเกือบทั้งปี ปัจจัยเหล่านี้ล้วนส่งผลและลดทอนประสิทธิภาพของแท่งหล่อลื่นที่ทำจากโมลิบดีนัมไดซัลไฟด์ จึงเป็นเหตุให้ทีมวิจัยต้องเสาะหาและพัฒนาหาทางเลือกอื่น จนสุดท้ายได้มาลงตัวกับวัสดุแกรไฟต์”
“แม้ว่าในแง่คุณสมบัติการทนต่อความสึกหรอ (wear resistance) อาจไม่เทียบเท่าผลิตภัณฑ์จากต่างประเทศ แต่ด้วยประสิทธิภาพโดยภาพรวมและการใช้งานที่เหมาะสมกับสภาพภูมิอากาศของไทย รวมทั้งราคาที่ย่อมเยากว่าอย่างมีนัยสำคัญ เท่านี้ก็เป็นเหตุผลที่เพียงพอแล้วในแง่ความคุ้มค่าและไม่ยากต่อการตัดสินใจให้หันมาเลือกใช้ นอกจากนี้การถอดเปลี่ยนชิ้นส่วนก็สามารถทำได้ง่าย”
คุณภาณุเปรียบเทียบให้เห็นภาพว่า “ลองจินตนาการตัวดินสอเปลี่ยนไส้ที่เป็นที่นิยมในสมัยก่อน เมื่อไส้ดินสอหดทู่ เราก็เพียงถอดเปลี่ยนโดยดึงตัวไส้จากด้านล่างแล้วไปเสียบที่ด้านบน เพื่อให้ตัวไส้อันใหม่เลื่อนลงมาทดแทน ซึ่งในกรณีของรถไฟการติดตั้งช่องใส่แท่งหล่อลื่นหนึ่งๆ จะสามารถรองรับได้ราว 4 ชิ้นเรียงต่อกัน”
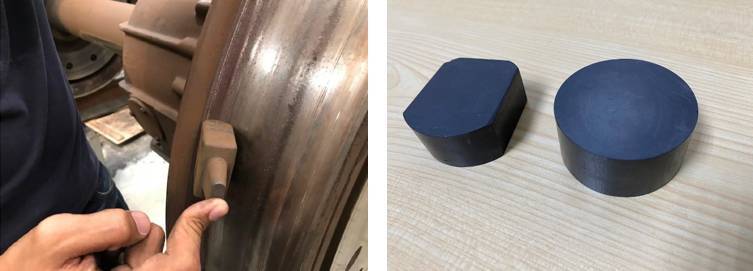
แท่งหล่อลื่นบังใบล้อแบบของแข็งสำหรับระบบราง (Solid lubricant sticks)
“มาถึงชิ้นส่วนตัวที่สอง ซึ่งทุกวันนี้ยังต้องนำเข้าจากต่างประเทศและมีราคาสูงมากเช่นกันคือ ชิ้นส่วนตัวนำคาร์บอนของแหนบรับไฟสำหรับรถไฟฟ้า (carbon strip of pantograph for electrical trains) ชิ้นส่วนนี้มาพร้อมกับโจทย์ยากและท้าทายกับทีมวิจัยมาก นั่นคือกระบวนการขึ้นรูป”
เพื่อให้เข้าใจชิ้นส่วนนี้ได้ดียิ่งขึ้น คุณภาณุได้ถอยกลับไปเริ่มที่ภาพใหญ่ของการทำงานสำหรับระบบจ่ายไฟฟ้าของรถไฟ ดังนี้ “รถไฟที่เราเห็นวิ่งกันอยู่ทุกวันนี้นั้น ไม่ได้มีเครื่องกำเนิดไฟฟ้าบนขบวนรถไฟเอง แต่ต้องอาศัยระบบจ่ายพลังงานไฟฟ้าจากภายนอกให้กับตัวรถไฟ โดยทั่วไประบบจ่ายไฟฟ้าจะมีอยู่ 2 รูปแบบคือ ระบบจ่ายไฟฟ้าเหนือพื้นดิน (Overhead Catenary System, OSC) ตัวอย่างที่มีใช้เช่น Airport Rail Link กับอีกแบบคือ ระบบจ่ายไฟฟ้าแบบใช้รางที่สาม (Third Rail System) ตัวอย่างที่มีใช้ก็เช่น BTS”
“สำหรับชิ้นส่วนแหนบรับไฟนั้นเป็นวัสดุอุปกรณ์ที่ถูกใช้สำหรับระบบจ่ายไฟฟ้าเหนือพื้นดิน (OCS) ซึ่งระบบนี้จะจ่ายพลังงานไฟฟ้าให้แก่ตัวรถผ่านสายไฟฟ้าที่อยู่บนเสาไฟฟ้าซึ่งตั้งคู่ขนานเรียงรายไปกับทางรถไฟ โดยกระแสไฟฟ้าจะไหลผ่านขารับกระแสไฟฟ้าที่ติดตั้งอยู่ด้านบนตัวรถไฟ ก่อนเข้าสู่ระบบขับเคลื่อนขบวนรถต่อไป ขารับที่ติดตั้งอยู่ด้านบนตัวรถไฟและแตะกับสายส่งที่ว่าก็คือ แหนบรับไฟ”
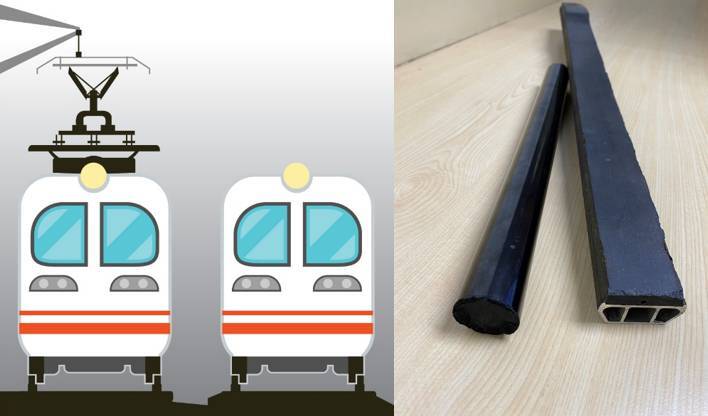
ชิ้นส่วนตัวนำคาร์บอนของแหนบรับไฟสำหรับรถไฟฟ้า (Carbon strip of pantograph for electrical trains)
ชิ้นส่วนนี้มีความยาวราว 1 เมตร และเนื่องจากมีหน้าที่เป็นตัวนำกระแสไฟฟ้าจากระบบจ่ายไฟฟ้าผ่านสายส่งตัวนำ (contact wire) เข้าสู่ตัวรถไฟ จึงทำให้เกิดการรับแรงและเกิดความร้อนขึ้นอย่างมหาศาล ส่งผลให้สึกหรอได้ง่าย ต้องถอดเปลี่ยนบ่อยครั้ง สำหรับในเชิงวัสดุทางทีมยังคงเลือกใช้ตัวกราไฟท์ที่ให้สมบัตินำไฟฟ้าที่ดี
อย่างไรก็ดี ประเทศไทยไม่ได้มีองค์ความรู้ด้านกระบวนการผลิตหรือเคยมีการพัฒนาชิ้นส่วนลักษณะนี้มาก่อน เอ็มเทคจึงถือเป็นหน่วยงานแรกๆที่ได้ออกแบบและพัฒนา ที่สำคัญใช้พื้นฐานข้อมูลการใช้งานและสภาพแวดล้อมจริงๆ ของประเทศไทย ทีมวิจัยของคุณภาณุ เลือกใช้กระบวนการผลิตแบบการอัดรีดแบบร้อน (hot extrusion) ซึ่งมีกรรมวิธีการอัดขึ้นรูปที่เหมาะสมกับลักษณะรูปร่างภายนอกของชิ้นส่วนนี้ โดยการลดพื้นที่หน้าตัดชิ้นงานลง แล้วบรรจุแท่งชิ้นงาน (billet) ภายในแม่พิมพ์ จากนั้นจึงอัดชิ้นงานให้ไหลออกผ่านปากแม่พิมพ์
สำหรับชิ้นส่วนรถไฟชิ้นสุดท้ายที่ทีมวิจัยพัฒนาขึ้นคือ แผ่นเบรกรถไฟจากวัสดุเชิงประกอบเนื้อทองแดง (brake pads from sintered self-lubricating composites) คุณภาณุอธิบายหลักการทำงานว่า “เพื่อห้ามล้อหรือเบรกให้รถไฟที่กำลังวิ่งอยู่เคลื่อนช้าลงจนกระทั่งหยุดนั้น จะอาศัยหลักการทำงานเดียวกันกับของรถยนต์ กล่าวคือเป็นการใช้แผ่นเบรกกดลงบนจานเบรกเพื่อให้เกิดแรงเบรกขึ้น และแรงเบรกดังกล่าวจะส่งกำลังไปหยุดล้อที่กำลังหมุนอยู่จนกระทั่งหยุดลง”
“ปกติแผ่นเบรกรถไฟของไทยในปัจจุบันนิยมทำจากเหล็กหล่อ (cast iron) ด้วยเหล็กชนิดนี้ให้คุณสมบัติเหนียวและแข็งแรงและราคาถูก ซึ่งสำหรับชิ้นส่วนนี้ประเทศไทยเราสามารถผลิตได้เอง การรถไฟมีองค์ความรู้และมีโรงงานเป็นของตัวเอง แต่ข้อเสียของแผ่นเบรกประเภทนี้คือ มีอัตราการสิ้นเปลืองที่สูง สึกเร็วทำให้ต้องเปลี่ยนใช้บ่อย แตกต่างจากแผ่นเบรกที่ทำจากวัสดุคอมโพสิต (composite material) หรือก็คือวัสดุที่เกิดจากการรวมตัวกันของวัสดุมากกว่าหนึ่งชนิดขึ้นไปแล้วทำให้สมบัติของวัสดุรวมดีขึ้น วัสดุคอมโพสิตให้สมบัติที่ดีกว่า น้ำหนักเบากว่า แต่ก็มาพร้อมกับราคาที่สูงกว่าด้วยเช่นกัน”
“ที่สำคัญประเทศไทยขาดองค์ความรู้ในการผลิตชิ้นส่วนดังกล่าว นอกจากนี้ปัญหาหนึ่งที่พบและถือเป็นโจทย์ใหญ่จากผู้ใช้อย่างการรถไฟโดยตรงก็คือ ปัญหากลิ่นไม่พึงประสงค์เกิดขึ้นขณะรถไฟเบรกเป็นต้นว่าขณะรถไฟกำลังเข้าเทียบชานชลา ซึ่งทีมวิจัยต้องทำการบ้านเพิ่มเติมในการศึกษาองค์ประกอบทางเคมี โดยเฉพาะการเสาะหาและปรับปรุงวัตถุดิบหรือเรซิน (resin) ที่เหมาะสม เพื่อไม่ให้เกิดหรือลดการปลดปล่อยกลิ่นลงด้วย
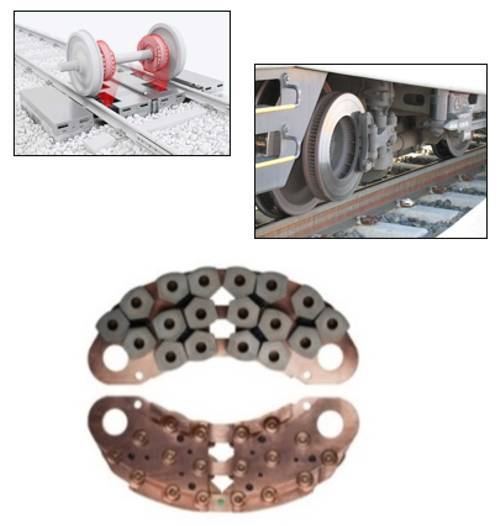
แผ่นเบรกรถไฟจากวัสดุเชิงประกอบเนื้อทองแดง (Brake pads from sintered self-lubricating composites)
นอกจากนี้สิ่งที่ทีมงานคุณภาณุและทีมวิจัยให้ความสำคัญอย่างยิ่ง เรียกได้ว่าขาดไม่ได้ก็คือ การทดสอบคุณภาพของตัวผลิตภัณฑ์ทั้งในแง่ประสิทธิภาพและความปลอดภัยตามแนวทางมาตรฐานสากล เพื่อให้เกิดความเชื่อมั่นและเป็นที่ยอมรับของผู้ใช้งาน โดยผลิตภัณฑ์ชิ้นส่วนรถไฟแต่ละชิ้นจะมีมาตรฐานที่ใช้อ้างอิงแตกต่างกันไป เป็นต้นว่า มาตรฐาน EN 16028:2012 ก็เป็นมาตรฐานในด้านประสิทธิภาพของตัวผลิตภัณฑ์แท่งหล่อลื่น เป็นต้น ทั้งนี้ปัจจุบันผลงานทั้งสามอยู่ในขั้นการขยายผลสู่การทดลองใช้จริงภาคสนาม
ความท้าทายที่รออยู่ข้างหน้า
ด้วยบริบทโลกในปัจจุบันทั้งด้านสังคมและเทคโนโลยีที่เปลี่ยนแปลงไป คุณภาณุฉายภาพต่ออุตสาหกรรมเหล็กไทยที่กำลังเผชิญความท้าทาย และกังวลกับข้อเท็จจริงที่พบว่า “ศักยภาพในการแข่งขันและกำลังการผลิตเหล็กของผู้ประกอบการไทยลดต่ำลง อุตสาหกรรมเหล็กถือเป็นหนึ่งในอุตสาหกรรมต้นน้ำและเป็นพื้นฐานของอีกหลายอุตสาหกรรมในไทย ที่ผ่านมาผู้ผลิตพยายามเน้นพัฒนาประสิทธิภาพการผลิตและแนวทางการทำธุรกิจมาโดยตลอด แต่ก็ยังประสบปัญหาที่แก้ไม่ตกไม่ว่าจะเป็นปัญหาการแข่งขันทางการค้าที่ไม่เป็นธรรม ปัญหาความไม่สมดุลระหว่างระดับความต้องการใช้และผลผลิต ปัญหาต้นทุนทางด้านพลังงานที่สูงขึ้น”
ทางออกทางหนึ่งคือการสนับสนุนผู้ประกอบการให้ปรับเปลี่ยนและพัฒนาตนเองในด้านกระบวนการผลิตให้เท่าทันกับบริบทโลกที่เปลี่ยนแปลงไป เป็นต้นว่า ตามแนวทางคำแนะนำของสภาอุตสาหกรรมแห่งประเทศไทยที่สนับสนุนการพัฒนากระบวนการผลิตจากปัจจุบันที่โรงงานผลิตเหล็กต้นน้ำของไทย หลอมเศษเหล็กด้วยเตาอาร์คไฟฟ้า (electric arc furnace) และเตาเหนี่ยวนำ (induction furnace) ก็ต้องปรับเปลี่ยนให้มีทางเลือกใช้ไฟฟ้าสีเขียว ซึ่งผลิตมาจากแหล่งพลังงานที่ไม่ใช่ฟอสซิล หรือส่งเสริมการใช้เทคโนโลยีอื่นที่ทันสมัยยิ่งขึ้น เช่น การผลิตเหล็กจากพลังงานไฮโดรเจน เป็นต้น เพื่อเพิ่มความสามารถในการแข่งขันให้สามารถส่งออกไปสหภาพยุโรป หรือสหรัฐฯ ซึ่งมีการส่งเสริมมาตรการด้านสิ่งแวดล้อมในลักษณะเดียวกันได้
ในทัศนะของคุณภาณุ กระแสการเปลี่ยนแปลงทางเทคโนโลยี จากยานยนต์เครื่องยนต์สันดาปภายในที่ประเทศไทยมีความชำนาญไปสู่ยานยนต์ที่ขับเคลื่อนด้วยไฟฟ้า ย่อมส่งผลกระทบต่อความต้องการชิ้นส่วนยานยนต์ที่ทำจากโลหะซึ่งมีทิศทางที่เปลี่ยนแปลงไป อุตสาหกรรมจะมีความต้องการวัสดุชนิดพิเศษเพิ่มมากขึ้น เช่น เหล็กกล้าความแข็งแรงสูงพิเศษ หรือวัสดุคอมโพสิตที่ให้คุณสมบัติด้านความแข็งแรงและน้ำหนักที่เบาลง หรือโลหะที่สามารถผ่านมาตรฐานความเข้ากันได้ทางแม่เหล็กไฟฟ้า (EMC) เป็นต้น
อีกทางเลือกที่น่าสนใจอย่างการประยุกต์ใช้เทคโนโลยีโลหะผง ซึ่งเทคโนโลยีนี้เป็นกระบวนการขึ้นรูปชิ้นงานโดยมีวัสดุตั้งต้นเป็นผง นํามาอัดให้ได้รูปทรงที่ต้องการแล้วนําไปให้ความร้อน เพื่อให้ผงและส่วนผสมอื่นประสานติดกันเป็นชิ้นงานของแข็ง เมื่อเปรียบเทียบกับกระบวนการผลิตแบบอื่นๆ แล้ว จุดเด่นประการหนึ่งของกระบวนการขึ้นรูปโลหะผงคือ ความสามารถในการผลิตชิ้นงานที่มีความซับซ้อนได้อย่างมีความเที่ยงตรงสูง ให้โครงสร้างจุลภาคสม่ำเสมอ และมีการใช้พลังงานของชิ้นส่วนที่ต่ำมาก
คุณภาณุจึงอยากฝากถึงผู้ประกอบการไทยที่สนใจ และประสงค์อยากต่อยอด หรือปรับเปลี่ยนตัวเองให้สอดรับกับทิศทางของเทคโนโลยีใหม่ๆ ที่เปลี่ยนแปลงไปว่า เอ็มเทคมีความพร้อมด้วยองค์ความรู้ ทักษะ และประสบการณ์ ตลอดจนบุคลากรที่มีความรู้ความชำนาญในหลากหลายสาขาเทคโนโลยีไม่ว่าจะเป็นเทคโนโลยีกระบวนการผลิตวัสดุโลหะผง กระบวนการผลิตแบบเติมเนื้อวัสดุ หรือเทคโนโลยีวัสดุอลูมิเนียมโฟมและโลหะผสม ซึ่งพร้อมที่จะเป็นส่วนหนึ่งในการช่วยให้การเปลี่ยนแปลงต่อยอดสู่ความสำเร็จและเพิ่มศักยภาพในการแข่งขันได้อย่างมั่นคงในอนาคต
แผนงานในอนาคต
ชิ้นส่วนหรือส่วนประกอบของรถไฟนั้นอาจกล่าวได้ว่ามีจำนวนมากมาย ขณะที่ชิ้นส่วนรถไฟทั้งสามส่วนที่คนไทยได้ร่วมแรงร่วมใจกันพัฒนาขึ้นนั้น เป็นเพียงจุดเริ่มต้นของการประกอบฟันเฟืองตัวแรกๆ หนทางไกลเริ่มต้นที่ก้าวแรกเสมอ ยังมีชิ้นส่วนอีกมากมายหลายชิ้นที่รอเราคนไทยในการพัฒนาต่อเนื่อง คุณภาณุมีความเชื่อมั่นว่าหัวรถไฟอย่างประเทศไทยมีความพร้อมและศักยภาพที่จะเติมเต็มช่องว่างตลอดจนพัฒนาให้รถไฟไทยพุ่งทะยานเดินทางไปได้อีกยาวไกล
แต่ความคาดหวังของคุณภาณุนั้น จะไม่เพียงแค่ภาพรถไฟที่โลดแล่นในผืนแผ่นดินไทยและใช้ชิ้นส่วนรถไฟที่ทำโดยฝีมือคนไทยแล้วเท่านั้น ยังจะหมายมั่นขยายไปถึงประเทศเพื่อนบ้านใกล้เคียงในภูมิภาคเอเชียตะวันออกเฉียงใต้ที่มีการใช้รถไฟฟ้าหรือรถไฟความเร็วสูง จะหันมาสนใจและกลายเป็นตลาดสำคัญสำหรับผู้ประกอบการชิ้นส่วนรถไฟของไทยในอนาคตต่อไป
สนใจพัฒนาผลิตภัณฑ์ติดต่อ
คุณพวงพร พันธุมคุปต์
งานประสานธุรกิจและอุตสาหกรรม ฝ่ายพัฒนาธุรกิจ
โทรศัพท์ 0 2564 6500 ต่อ 4784
อีเมล: puangpp@mtec.or.th
คุณกนกพร มั่นสกุล
งานประสานธุรกิจและอุตสาหกรรม ฝ่ายพัฒนาธุรกิจ
โทรศัพท์ 0 2564 6500 ต่อ 4305
อีเมล: kanokpom@mtec.or.th
ขอบคุณข้อมูลจาก
คุณภาณุ เวทยนุกูล นักวิจัย ทีมวิจัยเทคโนโลยีกระบวนการผลิตวัสดุผง กลุ่มวิจัยกระบวนการทางวัสดุและการผลิตอัตโนมัติ ศูนย์เทคโนโลยีโลหะและวัสดุแห่งชาติ (เอ็มเทค)
แหล่งข้อมูลอ้างอิง
ขอขอบคุณข้อมูลจาก
https://www.mtec.or.th/news-event/35232/
https://www.thairath.co.th/money/economics/analysis/2708048