Development of new quality control system in plastic part manufacturing by integration of machine vision technology and automatic box printing technology
Background
The accuracy of packaging process is one of basic indicators for quality of factories and business operations. Faulty labeling could harm reputation of the business operators. Random inspection cannot guarantee the correctness of packaging since the process still allows faulty labeling products to be released to the market. Automation technology that could inspect the package 100% could play a crucial role in building customer trust as well as enforcing transparency in the internal management within the manufacturing facilities.
Nawaplastic Industries (Rayong) Co., Ltd., which is an affiliate company of the Siam Cement Public Company Limited (SCG), wished to modernize their manufacturing process. With this target in mind, quality assurance throughout the production process of their packing process is crucial and must be efficient, accurate and done automatically. Moreover, the system should be ready for Industry 4.0.
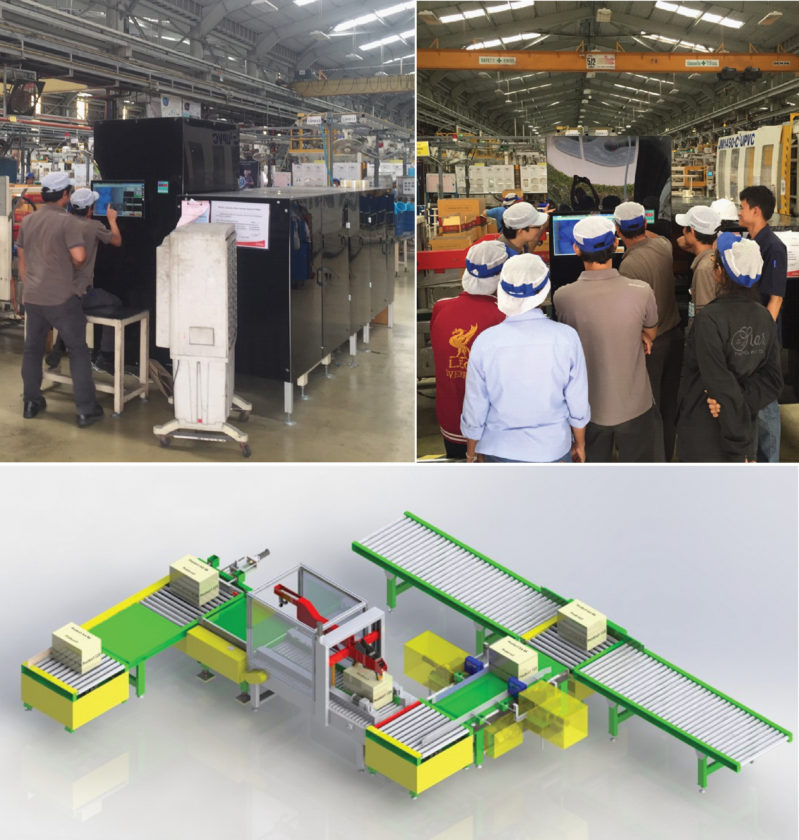
Targets
Development of a quality assurance system for packing process using machine vision technology (camera system and automatic software) which monitor the correctness of product packaging according to color code printed on the side of the box. The system must be able to evaluate the number of parts in each box using the weight information and print details of each product on the side of each box automatically through the use of images and machine learning software.
How does the research team do?
MTEC and Nawa Plastic engineering team work closely to define the machine specifications and the features necessary for a prototype. These machine specifications and the required features are then used in the design of internal mechanism, conveyor system, pneumatic system, electrical system, electronic system and sensors inside the machine as well as in the development of machine vision software.
The machine vision software is a crucial part of the prototype. The software acquires images from an industrial machine vision camera and processes these images using a technique called Sample-Based Identification (SBI), resulting in a system that can automatically identify the product that has been put in the box correctly. With the information given by the automatic product identification, a high-speed ink-jet printer prints details of each product on the box and then the machine automatically seals the top of the box.
Results
Our system can make a complete inspection of the correctness of product packaging, print the product details and seal the tops completely automatic. The inspection time along take less than 3 seconds. The new system developed could save three shifts of one operator.
Current situation
The prototype has been installed and been used in the actual production line at Nawa Plastic Industries (Rayong) Co., Ltd., located in Hemaraj Eastern Seaboard Industries Estate, Rayong province, since January 2017. The machine has helped control the quality of the packing process, increase the confidence of customers and improve the transparency of the internal management.
Outlook
The customer plans to transfer this technology to their other production facilities and to continue working with MTEC on new projects.